The day SpaceX successfully launched Crew 5, I sat down with Jon Edwards, the vice president of Falcon launch vehicles, for an exclusive interview at SpaceX headquarters.
At 43, he was younger than I expected, and quick-witted, with sharp, probing eyes. Four astronauts lifted off atop a new Falcon 9 that morning, which, Edwards told me, is always a little more stressful than when the company launches a flight-proven rocket.
When he started at SpaceX in 2004, the words “flight-proven rocket” would have seemed absurd, as there was no such thing. That previously-flown rockets are now considered the more reliable option is a testament to how far spaceflight has come in such a short time, and a large measure of credit for that goes to Edwards himself.
On launch days, which are increasingly common for SpaceX, which aims to achieve 100 such feats in 2023, every prospective problem must be worked doggedly. Two hours before he walked into the conference room for our interview, a computer flagged a payload fairing anomaly for a Starlink launch later that day. They would not be receiving live telemetry from the fairing in flight. Edwards investigated the glitch with the responsible engineer so they could find a way to contain the issue. He needed to know if the problem would affect the primary or secondary mission objectives, namely: the deployment of the Starlink payload, and the recovery of the fairings and booster.
Falcon 9 launches from Kennedy Space Center / John Kraus for Supercluster
“Sometimes in this business, a small, seemingly innocuous issue can actually be a symptom of a much bigger problem,” he said. “For every little issue that you see, you have to assume that it's bigger than you think it is until you're convinced otherwise. You've probably heard us say, ‘only the paranoid survive.’ That's what got us to where we are. I've been here a long time, and that one thing saved our butts time and time again.”
Edwards was hired right out of college by Tom Mueller, an aerospace engineer and one of the founders of SpaceX. In those days, SpaceX was not even blowing up rockets yet, let alone launching or landing them. Rather, the company was just beginning to do turbopump testing. Elon Musk was not yet a mega-celebrity and still did all job interviews himself.
“Even then, when he entered the room, it was an intimidating presence,” Edwards recalled. “He got right to it. He didn’t waste any time. He looked at my resume quietly, got up, asked me a few questions about projects I worked on in school, and asked me a riddle.”
(Edwards asked that I not share the riddle, just in case Elon still uses it. It involved geography and had more than one answer.)
Edwards gave a correct answer straightaway, and Elon replied, “OK, that’s the easy answer. What about the hard one?” So Edwards thought about it more and gave a very creative, but very wrong answer. Elon laughed at Edwards’ response but appreciated the young applicant’s out-of-the-box thinking.
Such thinking, along with that healthy dose of paranoia, would eventually launch—and eventually begin to land—the Falcon line of rockets.
And from the start, rocket recovery was part of Elon's plan.
“We put a parachute on the very first rocket we lost,” said Edwards. It was a long shot that the parachute would actually work (the rocket broke up during reentry before the parachute had a prayer), but, he continued, “Elon always has this thing where you have to have a greater-than-zero-percent chance. You don't put a parachute on it, there’s a zero-percent chance it survives.”
Eventually, the Falcon team decided to go for propulsive landings. It was ambitious, and though the idea suffered frequent public ridicule with each failure, inside SpaceX, no one thought the idea was impossible.
“I mean, it was within the laws of physics,” said Edwards. “We knew that the tricky part was having a rocket with extra performance to do its primary mission—which is to put a meaningful amount of payload mass in orbit—and then have the energy left over to propulsively land.”
Quick View: Falcon 9 Block 5
Height
70 m / 229.6 ft
Diameter
3.7 m / 12 ft
Mass
549,054 kg / 1,207,920 lb
Payload to LEO
22,800 kg / 50,265 lb
Payload to GTO
8,300 kg / 18,300 lb
Payload to Mars
4,020 kg / 8,860 lb
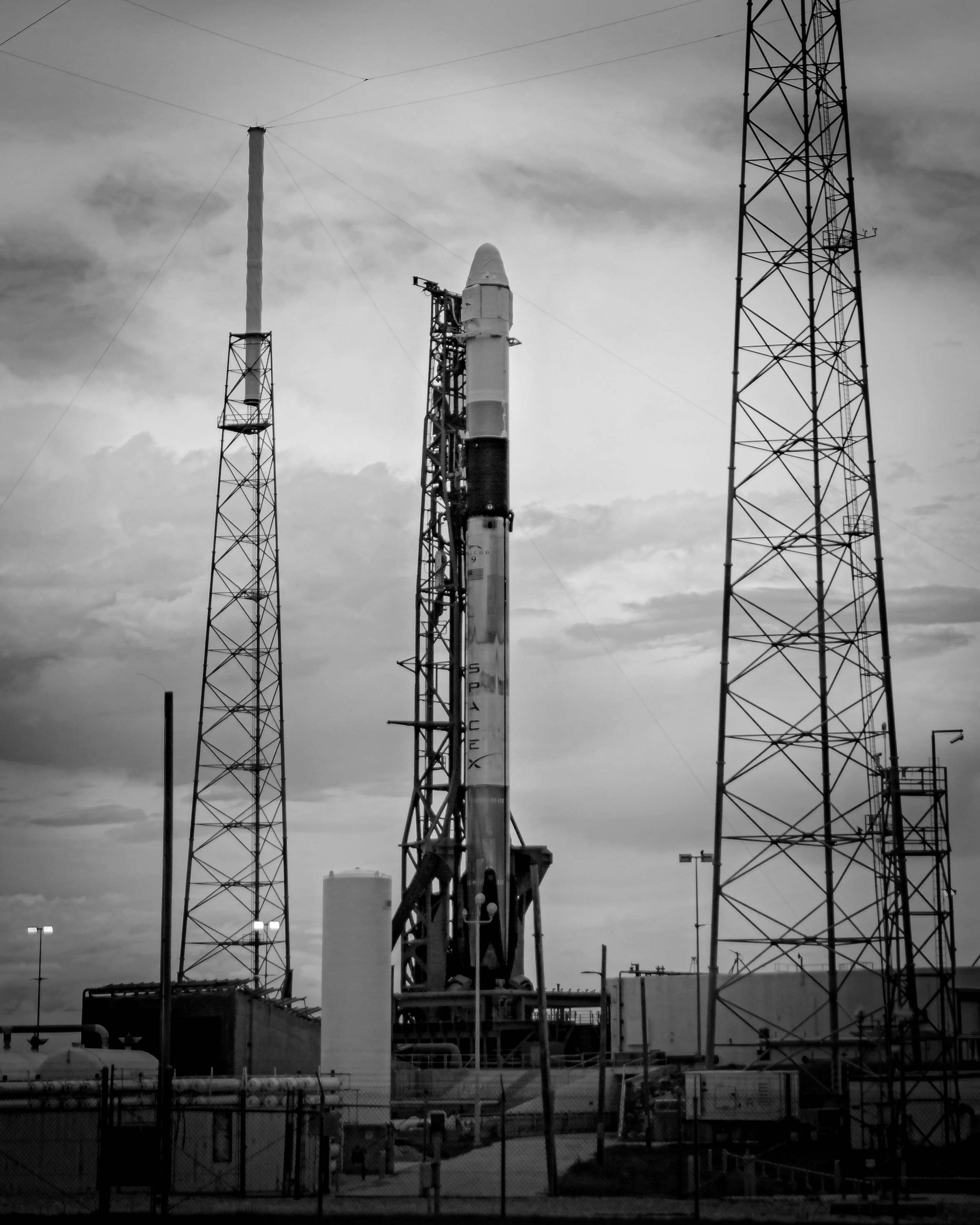
The first time SpaceX tested its soft landing systems on an actual mission was in 2013, after placing the Canadian CASSIOPE spacecraft in orbit. Rather than attempt to land on a drone ship, however, the rocket aimed for the ocean. After deploying its payload, the rocket reoriented itself, as we have come to expect today, and descended to a predetermined spot in the ocean. There, above the water, it slowed under controlled power.
“The fact that we could actually slow this thing down and in a controlled way, kind of hit a target, and know our velocity? We're all just like: put some landing legs on it! This is gonna work. I remember after that mission, I was over the moon. I was like, this is actually going to work.”
Falcon 9 lands at Vandenberg / Pauline Acalin for Supercluster
It did, and aside from the cost savings of reusing rockets—once considered a one-and-done technology—Edwards said it has given SpaceX a tremendous reliability advantage over its competitors. The majority of work the Falcon team does between flights does not involve actually changing anything, but rather, inspecting the hardware that just flew.
“We're trying to learn what we can,” he said. “That's one of the things about recover-and-reuse that's often overlooked: it's an incredible advantage in terms of reliability to get your hardware back and be able to look at it and learn stuff you didn't know or expect. I'm convinced that companies that don't recover their rockets have issues they don't know about that someday will bite them.”
He believes that, in keeping with the SpaceX ethos of making rocket launches as regular and reliable as commercial air travel, “flight-proven” rockets will one day—if they are not already—be considered to be safer than flying a new rocket.
“Just like when they build an airplane, they do a test flight not with an entire load of people, but rather, two pilots alone who work it through the paces. It's similar to a rocket,” he said. “We would like to fly it first to really, really exercise it.”
F9 Inspiration4 Nebula / Erik Kuna for Supercluster
Since the start of the Falcon 9 reusability program, those exercises have extended the lifespan of that class of rockets from ten launches to, currently, twenty. The key to expanding reuse, he said, is “qualification,” which is an aerospace engineering term that basically means that analyses and testing have proven the margins for whatever a rocket needs to do in flight. “If you're going to do 20 launches, we have to show—either through analysis or tests or both—that you can do a lot more than that… We don’t just roll the dice.” He and his team spent an entire summer going through 500 different design units on the rocket, making sure every single one was fully qualified for the additional flights.
Support Supercluster
Your support makes the Astronaut Database and Launch Tracker possible, and keeps all Supercluster content free.
SupportInitial qualification for the Falcon Heavy rocket, also under his purview, was its own challenge from a structural dynamics perspective. The Falcon team had to figure out the interaction between the three boosters at liftoff, and their interaction with the launch pad. Booster separation was a particularly difficult problem to be solved and involved determining the loads going into the side boosters and the center core during separation so that all three would survive and still be reusable. The aerodynamics of the Falcon Heavy were also unique. Moreover, the Falcon team had to figure out the dangers of ice falling from the second stage and hitting the nosecones below. They even added carbon fiber armor to rocket protuberances to protect it from any high-altitude birds that might impact the rocket.
“By the time the rocket got to that altitude, an impacting bird would have hit as though it were shot from a cannon," Edwards explained. "We actually did some bird testing with frozen chickens.”
Launch is hard, reentry is hard, and landing is hard, but the biggest challenge with the Falcon 9 rocket that people do not necessarily expect, said Edwards, is what happens after it lands on a drone ship. “There are waves and there is wind. A storm can come through, and we can’t put people on there with a rocket slipping and sliding around.” The team developed a robot, called Octograbber, but it is not always agile or fast enough to grab a sliding rocket. “Ocean weather is intense, and we've had rockets slipping and sliding, and man, you just stay up all night praying it doesn't fall over the edge or something.”
Falcon 9 launches from Cape Canaveral / John Kraus for Supercluster
As for the future of Falcon 9 and Falcon Heavy, Edwards said there are no plans to make any further major changes to the rocket. Rather, the rocket team is focused on making small changes to improve reliability and rapid reusability.
“I think the fastest we’ve turned a booster around and launched it again is 21 days from launch to launch—and we can beat that,” he said.
Falcon 9 launches from Cape Canaveral / John Kraus for Supercluster
Another executive with the company said that during a recent Falcon 9 meeting, the team was discussing how to reduce refurbishment times, and how what used to take six months became five months became three months became three weeks. Elon chimed in: “Why do we have any refurbishment at all? We shouldn't need any refurbishment. You should just land it and fly it again—fix it so it does that.” It would involve evaluating all the things that presently require inspections between launches, and redesigning them so that said inspections are unnecessary. It is an ambitious goal, but if any company can pull off such a feat, it is SpaceX, which has a demonstrable record of doing the impossible-adjacent.
“The SpaceX approach is proven effective,” said Edwards. “If protecting the primary mission objective, you can take risks on the secondary mission. And it's okay to get some egg on your face. That's how you learn. Whereas other organizations want it to be perfect from the very first attempt, I promise you that you're going to learn twice as much by flying it than you are by pencil whipping and doing analyses. Because we sure did.”
Ultimately, according to Edwards, the imperative to optimize and improve with such ambition comes straight from the top of the company. “Elon says if you’re not putting holes in the ground, you're not trying hard enough.”
Twin Falcon 9 boosters lands at Cape Canaveral / Jenny Hautmann for Supercluster
David W. Brown is the author of THE MISSION, or: How a Disciple of Carl Sagan, an Ex-Motocross Racer, a Texas Tea Party Congressman, the World's Worst Typewriter Saleswoman, California Mountain People, and an Anonymous NASA Functionary Went to War with Mars, Survived an Insurgency at Saturn, Traded Blows with Washington, and Stole a Ride on an Alabama Moon Rocket to Send a Space Robot to Jupiter in Search of the Second Garden of Eden at the Bottom of an Alien Ocean Inside of an Ice World Called Europa (A True Story). He lives in New Orleans.